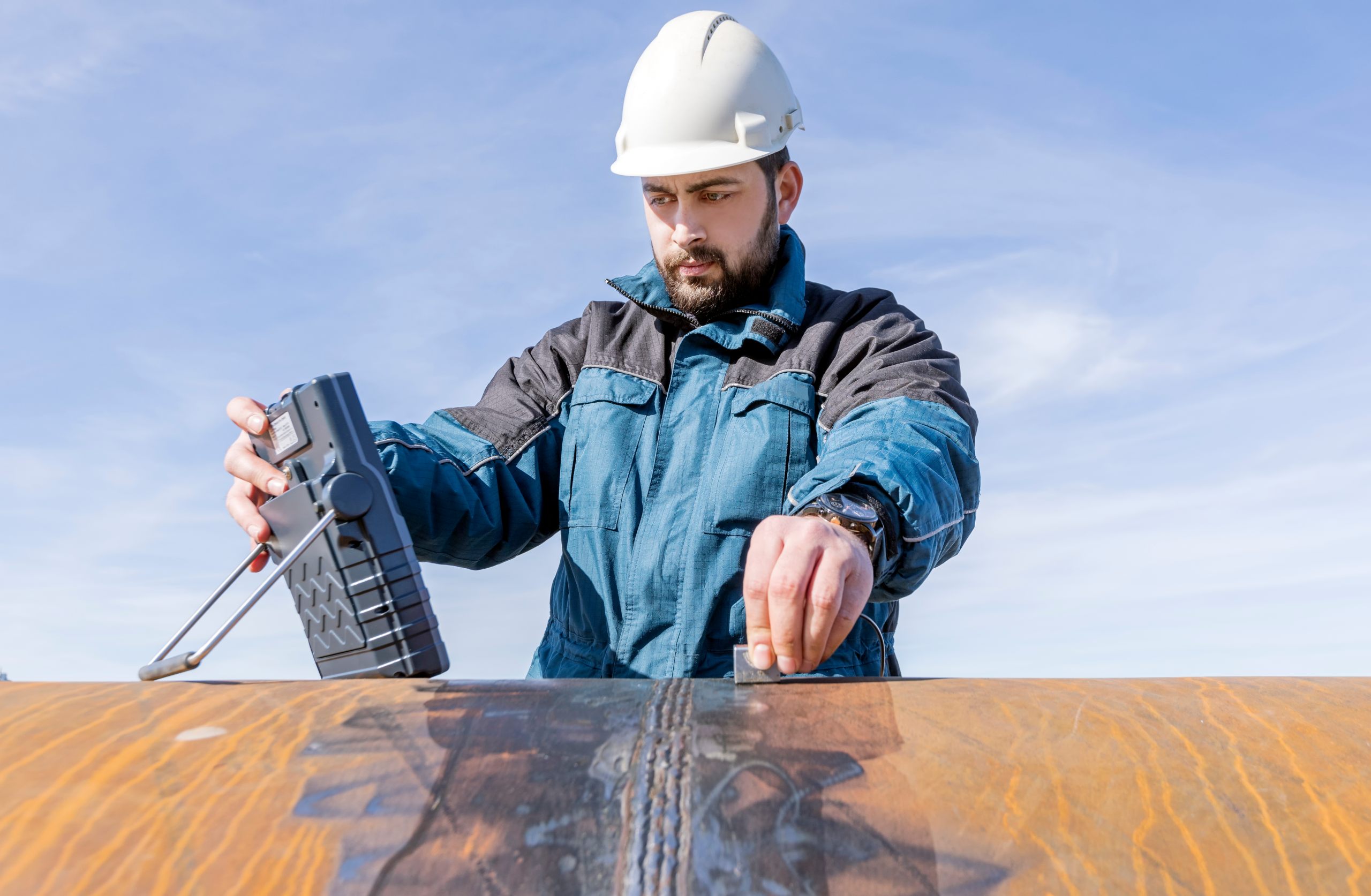
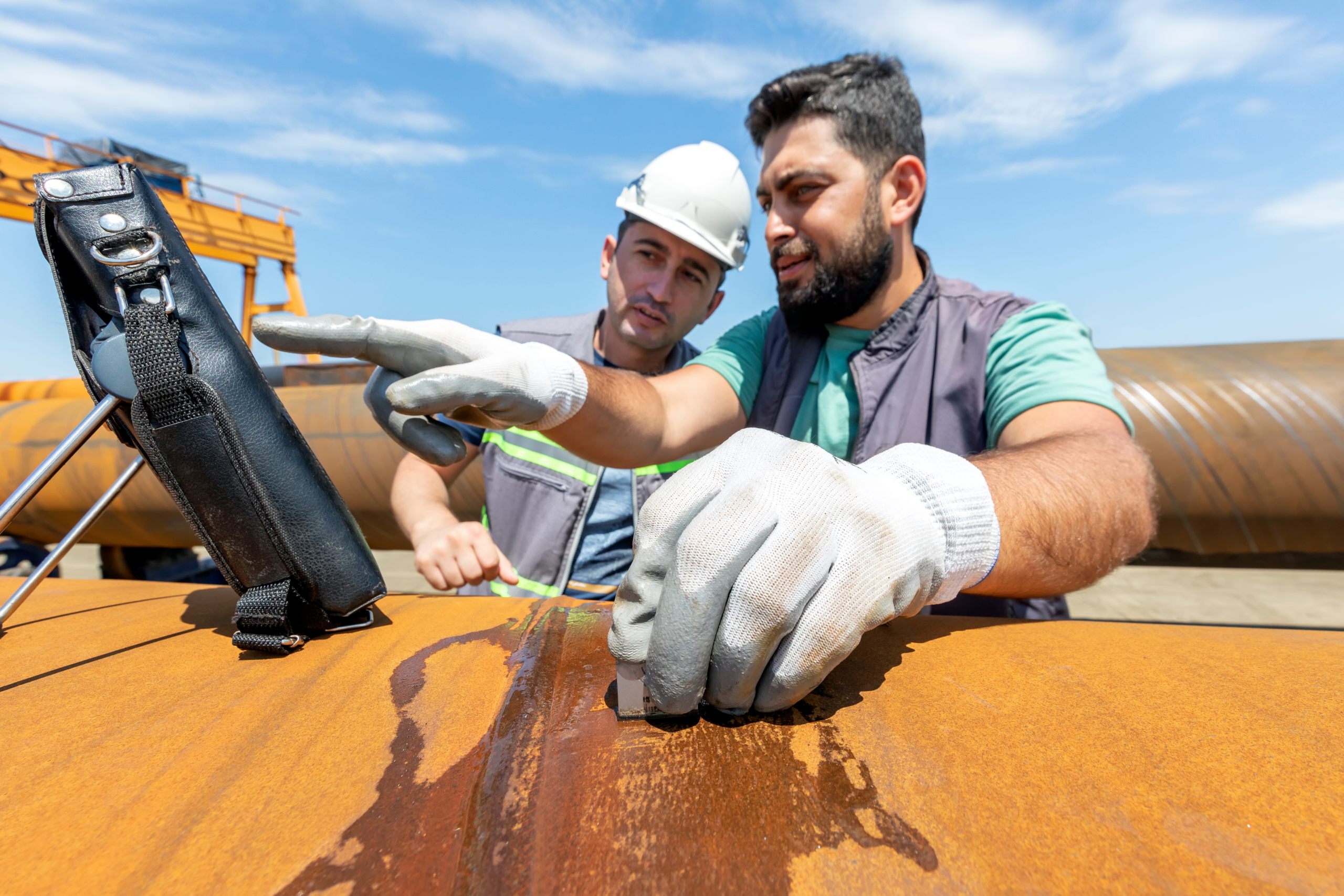
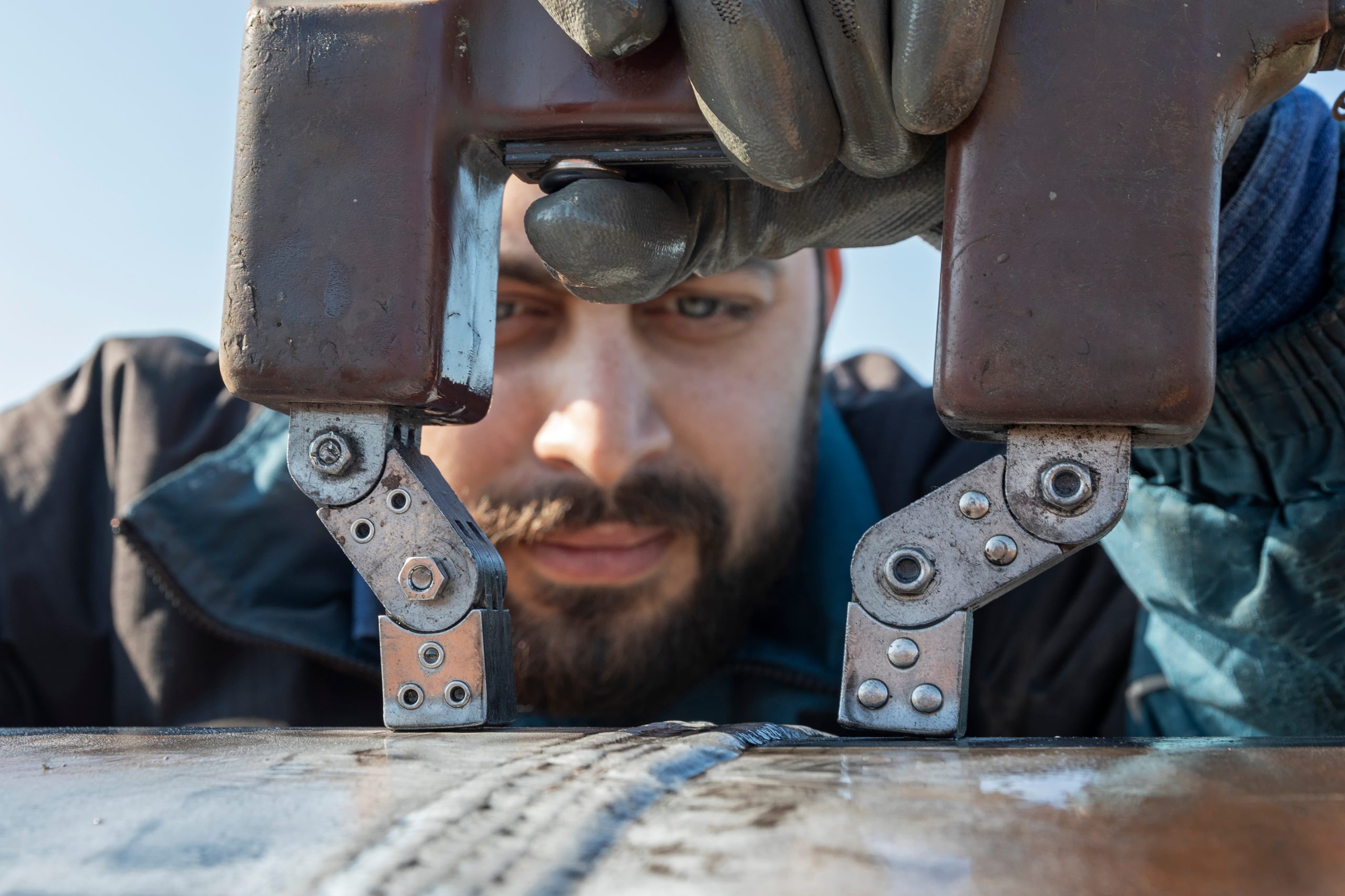
CELEBRATING 50 YEARS IN NDT & INSPECTION
Comprehensive Range of Inspection & Engineering Services
Welcome to IPEC Inspection Ltd., a fully Irish owned and operated engineering & inspection company based in Co. Cork since 1973. We are a leader in Welding Inspection & Non-Destructive Testing (NDT) solutions that redefine safety, reliability, and precision across industries. With an unwavering commitment to excellence, we stand as your trusted partner in ensuring the integrity of materials, structures, and components without compromise.
At IPEC, we understand that the quality of your products, projects, and operations is non-negotiable. Our NDT & Engineering expertise empowers you to make informed decisions, prevent failures, and optimize performance, all while reducing downtime and cost. We approach asset health impartially with an experienced led, integrity based approach and with a team of seasoned NDT professionals and cutting-edge technology at our core, we offer a comprehensive suite of services tailored to your every need.
Our Expertise
Backed by decades of collective experience, our experts are well-versed in a wide array of NDT techniques. From phased array ultrasonic testing to radiographic examination, magnetic particle inspection to positive material identification (PMI), eddy current testing to advanced 3D digital solutions, we deliver insights that transcend the surface and penetrate the heart of your materials and structures.
We understand that every project is distinct. That’s why we collaborate closely with you to develop custom-tailored NDT strategies that align with your specific goals. Our solutions seamlessly integrate into your workflow, ensuring minimal disruption while maximizing the accuracy of our assessments.
Cutting-Edge Technology
In a rapidly evolving technological landscape, we stay ahead of the curve. By harnessing the power of innovative tools, software, and equipment, we provide you with NDT solutions that are not only accurate but also efficient and future-ready.
Industry Impact
From pharmaceuticals to manufacturing, energy to construction, our impact spans across sectors. We’ve been instrumental in ensuring the safety of critical infrastructure, optimizing manufacturing processes, and bolstering the performance of vital components.
Collaborative Approach
We don’t just deliver results; we foster partnerships. Your success is our success, and we are dedicated to working closely with you, addressing your challenges, and celebrating your achievements.
How can we help?
We offer Non Destructive Testing (NDT), Advanced NDT, Pipework & Vessel Inspection, Welding Inspection & Certification, Asset Owner Consultation, 3rd Party Vendor Assessment, Coating & Painting Inspection, Corrosion Assessment, Engineering & Pipeline Management Services, Pipeline Defect Assessment & Quality Assurance to ensure all our clients have complete confidence in their industrial assets.
Our team of highly skilled engineers & inspectors are experts in their field which helps ensure operational reliability & optimises performance across a wide range of operations. We believe our wealth of experience maintains a safe & productive asset assessment system for our clients here in Ireland and abroad.
INSPECTION & ENGINEERING SERVICES
Our Fields of Expertise
INSPECTION & ENGINEERING SERVICES
Speciality Services
- Non Destructive Testing (NDT)
- Vessel Inspection
- 3rd Party Vendor Assessment
- Pipeline Management & Supervision
- Advanced NDT
- Quality Assurance
- Pressure System Regulation Inspections (PSR’s)
- Coating, Painting & VS02 Inspections
- Welding Inspection & Certification
- Corrosion Assessment & Analysis
- 3D Laser Scanning & Assessment
- Asset Owner Consultation
INDUSTRIES WE DELIVER OUR SERVICES TO
Industry Sectors
Pharmaceutical
Oil & Gas
Power Generation
Construction
Petrochemical
Refining
IPEC Management
OUR TEAM
Michael Murphy
Managing Director
Dan Hallissey
Managing Director
Brendan Creedon
Gas Networks Operations Manager
(Southern & Western Region)
James Murphy
NDT Operations Manager
Projects Manager
Chris Dillon
Gas Networks Operations Manager
(Eastern Region)
Gerard Creedon
Contracts Manager
Angela O’ Rourke
Admin / Sales
Rebecca O’ Donovan
Accounts / HR